Case Studies in Smart Manufacturing: 5 AI Success Stories
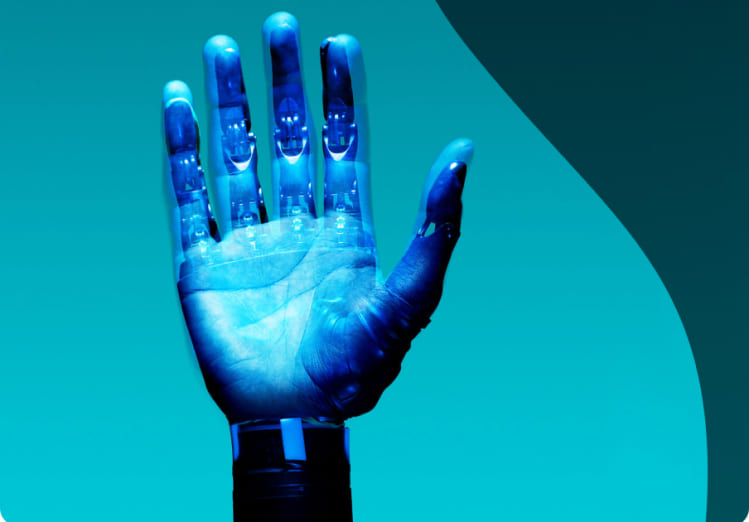
The factory floor of yesterday is rapidly becoming a relic. Today’s manufacturing powerhouses aren’t just experimenting with artificial intelligence – they’re using it to drive measurable improvements in efficiency, quality, and innovation. Let’s explore five real-world examples where AI is delivering tangible results right now.
Supply Chain Optimization: From Chaos to Clarity
When a major plumbing equipment manufacturer faced the challenge of optimizing their complex supply chain from Chinese factories to U.S. distribution points, they turned to ELEKS for an AI solution. The traditional approach of managing multiple warehouses, shipping routes, and delivery schedules across states had become too complex for human planners to optimize effectively.
ELEKS developed an AI-powered system that could analyze every aspect of the supply chain – from seaport selections to warehouse locations, from container packing to last-mile delivery routes. The system processes millions of data points to make decisions that would take human planners weeks to analyze, while continuously learning and adapting to changing conditions.
More importantly, the AI system’s intelligent routing and distribution decisions created a more resilient supply chain, reducing idle time at warehouses and optimizing inventory levels across their network.
Generative Design: AI as the Ultimate Creative Partner
General Motors is pioneering the future of automotive design through AI. As the first major automaker in North America to adopt Autodesk’s generative design software, GM is pushing the boundaries of what’s possible in vehicle lightweighting.
The AI-based system generates over 150 valid design options based on real-world constraints and performance requirements. In a proof-of-concept project at GM’s Tech Center in Warren, Michigan, engineers used this technology to reimagine a seemingly simple component – the seat bracket where seat belts are fastened.
while consolidating eight different components into a single 3D-printed part. For GM, this isn’t just about one component – it’s about transforming how they develop their next generation of vehicles, including their alternative propulsion and zero-emission lineup.
Energy Management: The Silent Efficiency Booster
In energy-intensive manufacturing sectors, AI is the new secret weapon for sustainability and cost reduction. Google demonstrated this dramatically when they applied DeepMind’s machine learning to tackle their massive data center cooling challenges.
The AI system processes data from thousands of sensors monitoring temperatures, power consumption, pump speeds, and other variables. By understanding these complex interactions, the neural networks can predict future efficiency metrics and make real-time adjustments that human operators might miss. The system adapts to changes in the environment and learns to optimize operations without relying on preset rules.
Even more impressive, this was achieved in Google’s already highly optimized data centers, which were previously getting 3.5 times more computing power from the same amount of energy compared to five years ago. It’s a powerful demonstration of how AI can transform energy management in any industrial setting.
Quality Assurance: The Relentless Perfectionist
Landing AI tackled a critical challenge at a refrigeration compressor manufacturer, where quality control meant submerging each unit in water while inspectors searched for telltale air bubbles indicating leaks. The traditional process was time-consuming and prone to human error, with inspectors struggling to maintain consistent accuracy throughout long shifts.
Developed under Andrew Ng’s leadership, Landing AI’s machine vision system revolutionized this process with sophisticated computer vision that detects bubbles with unprecedented accuracy. The system processes multiple video frames to distinguish between actual air leaks and manufacturing artifacts, using special lighting and QR code calibration to ensure optimal detection conditions.
With just 3% of cases flagged for human review, Landing AI’s solution dramatically reduced the inspection burden while improving accuracy, allowing manufacturers to redirect valuable human expertise to more complex tasks.
Manufacturing Intelligence: The Command Center of Operations
Yates Industries, a precision machinery manufacturer founded in 1972, faced a common modern challenge: plenty of data but not enough insight. With decades of manufacturing expertise and multiple data systems, they had mountains of information but struggled to turn it into actionable intelligence. Their transformation story with Seraf demonstrates the power of unified manufacturing intelligence.
By implementing Seraf’s Manufacturing AI Platform, Yates connected their disparate data sources into a single, intelligent system. The platform didn’t just collect data – it unified information from across their operation, from production floor sensors to quality control systems, making it instantly accessible through natural language queries. This meant everyone, from operators to executives, could get immediate answers to their manufacturing questions.
But perhaps more importantly, they transformed how their teams work. Instead of spending hours searching through different systems for answers, their people now focus on using insights to drive improvements. What started as a data integration project became a complete transformation of their manufacturing operations.
The Future is Now
This isn’t a glimpse into some distant future. These AI applications are transforming manufacturing floors today. They’re boosting efficiency, driving innovation, and changing how we work. But make no mistake – this revolution isn’t about replacing human workers. It’s about augmenting human capabilities, freeing up our time and brainpower to focus on what we do best: innovate, problem-solve, and drive progress.
Seraf combines all these AI capabilities into one unified solution. From predictive maintenance to quality control, supply chain optimization to energy efficiency, our manufacturing AI platform transforms your raw data into actionable intelligence. Built on 15 years of industry expertise, Seraf helps you drive innovation and efficiency across your entire manufacturing operation.
Book your Seraf demo today and begin your journey to smarter, data-driven manufacturing.
Get valuable insights about AI and business automation
Rely on Seraf, AI that consolidates all your systems
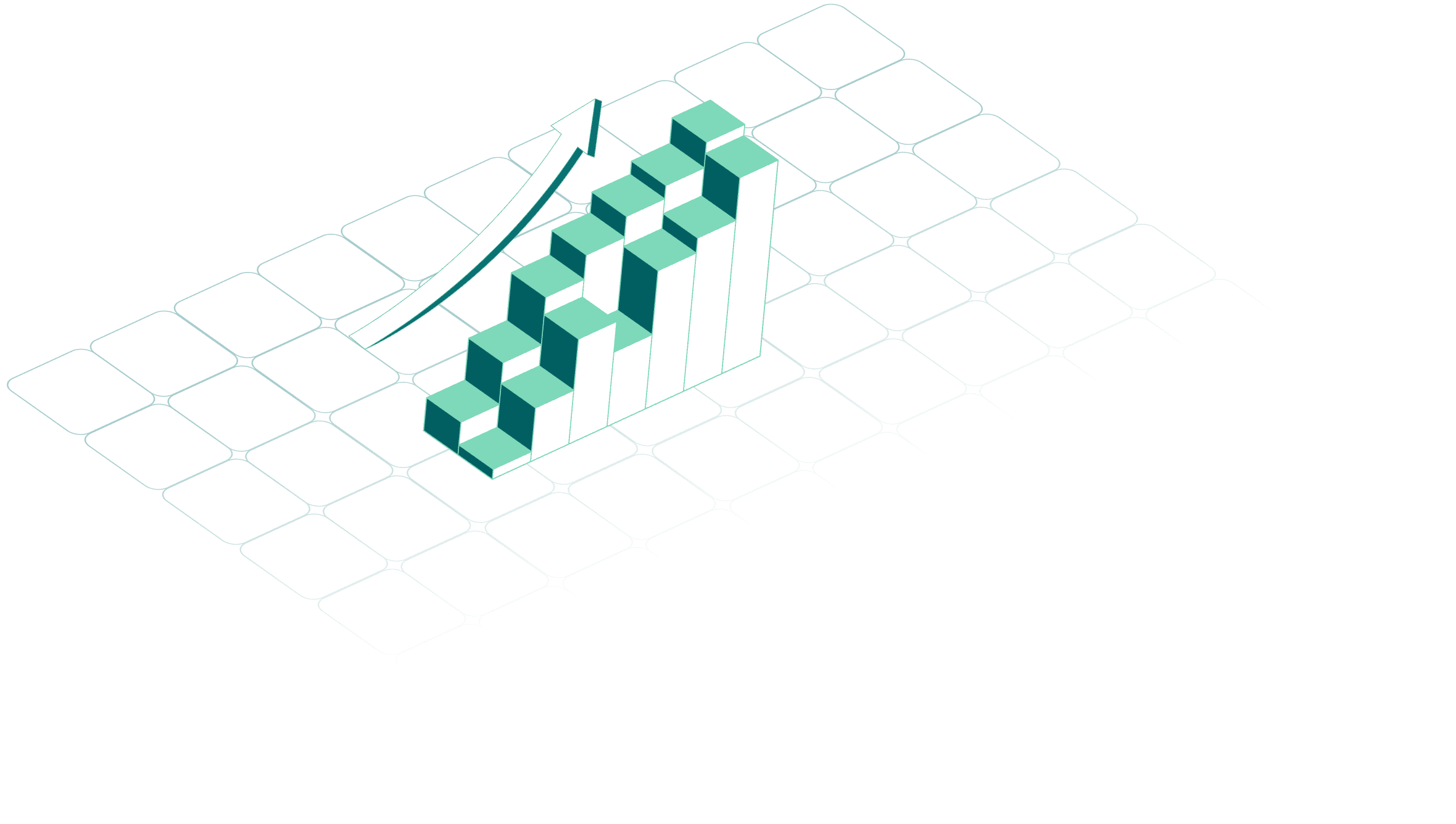