Back
Manufacturing Process Automation: Manufacturing Chatbots Are Paving the Way for Industry 4.0
AI for manufacturing is transforming Industry 4.0 adoption. Learn how manufacturing process automation saves manufacturers hundreds of hours monthly while connecting siloed information from shop floor to C-suite.
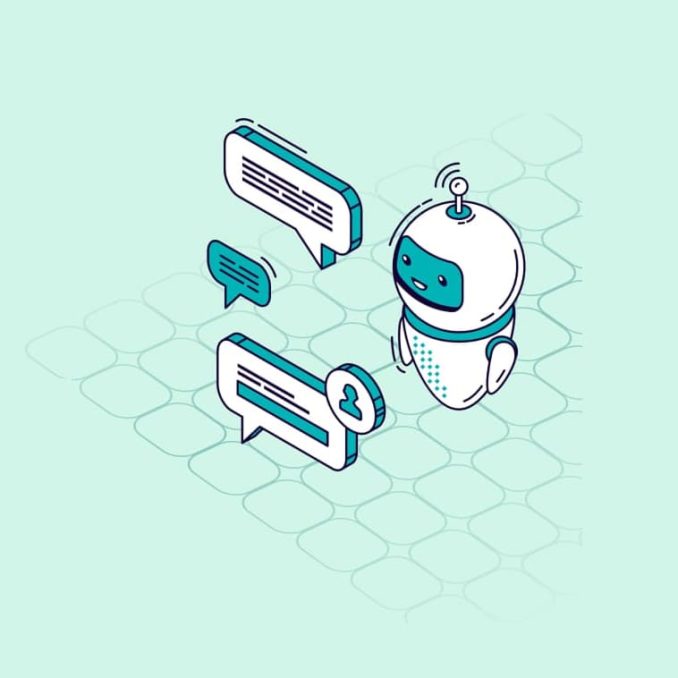
Manufacturing AI chatbots are shaking up the manufacturing world, making Industry 4.0 more connected and smarter than ever.
With the potential to save employees hundreds of hours every month, chatbots are breaking communication barriers on both the production floor and executive offices.
Like most companies, siloed information is a real bottleneck when it comes to efficiency and ultimately, profits for manufacturers.
Hunting for information or answers, whether by an entry level person or up to a C-level is a real inhibitor to getting the job done.
From managing orders to automating customer support, AI chatbots help everyone on the team get key business insights by simply asking a question.
Let’s take a look at some of the use cases for generative AI in manufacturing.
01. Order status inquiry
AI chatbots seamlessly integrate with your manufacturing software, offering real-time updates on order status for different products and parts. By interfacing with the system, they provide accurate and timely information, eliminating the need for manual tracking. This makes sure that users have precise insights into the order progress, promoting efficiency and transparency in the production workflow. Example:- Question: “Hey, can you check the status of the order for lead-acid batteries.? When is it expected to be shipped?”
- Answer: “The order for lead-acid batteries is currently in the final stages of processing and is scheduled to be shipped by the end of this week. You can expect it to reach its destination within the next 7-10 business days.”
02. Inventory availability
Another application for AI chatbots in manufacturing is their ability to scour inventory for product parts and raw material. This helps with informed decision-making for the upcoming production cycle. By centralizing this information, the chatbots contribute to strategic planning, minimizing the risk of shortages and optimizing inventory management. Example:- Question: “What’s the current availability of raw materials in the inventory? Are we well-stocked for the upcoming production cycle?”
- Answer: “Absolutely. As of now, our inventory shows a healthy stock of raw materials, ensuring that we are well-prepared for the upcoming production cycle. There are no anticipated shortages, and the available quantities should comfortably meet the production demands.”
03. Asking about shift schedules
Manufacturing is notorious for shift changes and updates. An AI chatbot can integrate with a manufacturing software to deliver comprehensive details about your upcoming shift schedule. Example:- Question: “Can you provide details about my upcoming shift schedule? Any changes or updates I need to be aware of?”
- Answer: “Certainly. Your upcoming shift schedule remains unchanged, with your regular shifts as per the established roster. There are no updates or alterations at this time. If you ever need to make adjustments or have specific preferences regarding your schedule, feel free to communicate with your supervisor. We prioritize employee satisfaction and work-life balance.”
04. HR policy clarification
AI chatbots act as knowledgeable resources for HR-related inquiries, accessing information from your internal databases. They can provide clear details about vacation policies, including the allotted days and the process for requesting time off. This streamlined access to HR information helps with a smoother and more transparent employee experience. Example:- Question: “I have a question about the vacation policy. How many days am I allowed, and what’s the process for requesting time off?”
- Answer: “Absolutely. According to our vacation policy, employees are entitled to 15 vacation days per year. To request time off, kindly submit your request through our HR portal at least two weeks in advance. The process ensures smooth coordination and allows us to accommodate your preferences whenever possible.”
05. Machine maintenance schedule
By providing details on upcoming tasks, AI chatbots can assist you in proactive maintenance planning. This helps to guarantee optimal machine performance and minimizes disruptions in the production process, contributing to operational efficiency. Example:- Question: “When is the next scheduled maintenance for the grid casting machine? Are there any upcoming maintenance tasks I should be aware of?”
- Answer: “Great question! The next scheduled maintenance for the grid casting machine is set for next Monday, between 9:00 AM and 12:00 PM. During this time, the machine will undergo routine checks and minor adjustments to ensure optimal performance. There are no additional maintenance tasks scheduled in the immediate future. If you notice any irregularities or have concerns, please report them to our maintenance team promptly.”
06. Product quality information
AI chatbots serve as valuable resources for accessing information on quality control measures. By interfacing with the manufacturing software, they can offer comprehensive details on the testing processes for the new product line. This facilitates a clear understanding of quality standards and procedures, promoting adherence to rigorous quality assurance protocols. Example:- Question: “What are the quality control measures in place for the new product line? Can you provide details on the testing process?”
- Answer: “Certainly. Our new product line undergoes rigorous quality control measures. The testing process includes thorough inspections at various production stages, ensuring adherence to quality standards. Additionally, random sampling is conducted for in-depth assessments.”
07. Safety protocol reminders
Safety awareness is of key importance in manufacturing. By providing reminders about safety protocols for operating different machines and production runs, AI chatbots contribute to a culture of safety within the manufacturing environment. This ensures that employees are well-informed and compliant with established safety guidelines. Example:- Question: “Could you remind me of the safety protocols for operating cell winders? Anything specific I should keep in mind during today’s production run?”
- Answer: “Absolutely. Safety is our top priority. When operating cell winders, please ensure that you wear the provided protective gear at all times. Be mindful of the emergency stop procedures, and refrain from bypassing any safety mechanisms. Today’s production run involves handling slightly elevated temperatures, so exercise caution and stay hydrated. If you observe any safety concerns or require assistance, don’t hesitate to contact our safety officer or your supervisor immediately.”
08. Training program access
Guiding employees through the process of accessing training modules can be time consuming and complex. By providing information on the specific platform or portal for the latest training related to new equipment installation, AI chatbots facilitate a smooth and efficient learning experience. This ensures that employees have easy access to essential training resources, promoting skill development and proficiency in equipment operation. Example:- Question: “How can I access the latest training modules for the new equipment installation? Is there a specific platform or portal I should use?”
- Answer: “Certainly. The latest training modules for the new equipment installation are available on our training portal accessible through the company intranet. Simply log in with your credentials, navigate to the training section, and you’ll find the modules categorized for easy access. If you encounter any issues or have further questions, our IT support team is available to assist you. Happy learning!”
09. Employee benefits overview
AI chatbots act as reliable sources for accessing information on employee benefits. This includes providing a concise overview of the employee benefits package. Additionally, they can communicate any recent updates or changes, ensuring that employees stay well-informed about their benefits and fostering transparency in HR communication. Example:- Question: “Can you give me a quick overview of the employee benefits package? Any recent updates or changes I should be aware of?”
- Answer: “Absolutely. Our employee benefits package includes health insurance, retirement plans, and annual wellness programs. There have been no recent updates or changes to the existing benefits. However, we encourage employees to regularly check the HR portal for any announcements or policy updates. If you have specific inquiries about your benefits or need personalized assistance, our HR team is available to guide you.”
10. Production efficiency tips
AI chatbots are designed to offer valuable insights into enhancing production efficiency. The best use case here is providing practical suggestions to streamline workflow on the assembly line. Example:- Question: “Do you have any suggestions for improving production efficiency on the assembly line? I’m looking for tips to streamline our workflow.”
- Answer: “Certainly. One effective way to improve efficiency on the assembly line is by conducting periodic training sessions to ensure that all team members are familiar with the latest processes and techniques. Additionally, consider implementing a visual management system to enhance workflow visibility. Regular maintenance of equipment and proactive identification of potential bottlenecks can also contribute to streamlined operations. If you have specific areas you’d like to address or explore further, feel free to ask me!”
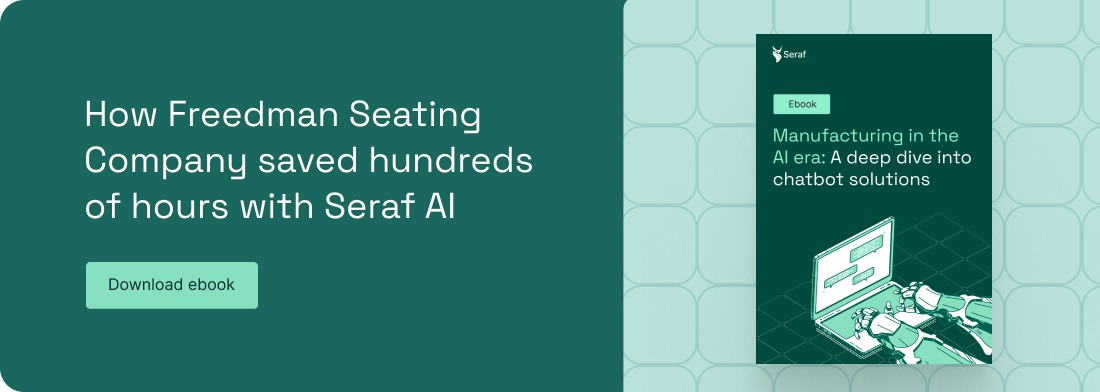