Back
Manufacturing Knowledge Management: Onboarding Best Practices
First impressions count in manufacturing onboarding. Learn how effective manufacturing knowledge management systems streamline training, improve retention, and transform new hires into productive team members using lessons from industry leaders.
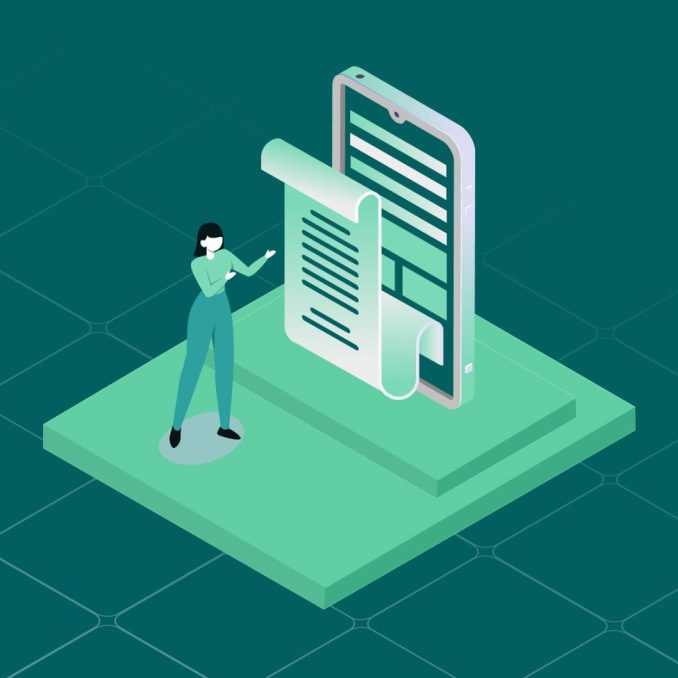
HR teams know better than anyone that first impressions count, and nowhere is this truer than in the world of employee onboarding.
Think about it: a new hire’s first days and weeks set the tone for their entire journey with your company.
Get it right, and you’re on your way to building a loyal, productive team member. Miss the mark, and well, you might just be restarting that hiring process sooner than you’d like.
What is Manufacturing Knowledge Management in the Most Basic Terms?
Manufacturing Knowledge Management is the systematic process of capturing, organizing, and sharing critical information within a manufacturing organization to improve efficiency, productivity, and decision-making. In its most basic terms, it involves:- Collecting valuable knowledge from various sources, including employee expertise, production processes, and historical data.
- Organizing this information in a centralized system for easy access and retrieval.
- Sharing the knowledge across the organization to solve problems, streamline operations, and drive innovation.
- Applying the shared knowledge to enhance manufacturing processes, product quality, and overall operational efficiency.
What Does Manufacturing Knowledge Management Have to do With Onboarding?
Manufacturing Knowledge Management and onboarding are closely interconnected, with knowledge management systems playing a crucial role in streamlining and enhancing the onboarding process for new manufacturing employees. Knowledge management systems provide centralized repositories where new hires can access training materials, standard operating procedures, safety protocols, and best practices. This accessibility accelerates learning and reduces the typical 1-3 month period needed for operators to reach full productivity. The benefits of integrating knowledge management into manufacturing onboarding include:- Faster time to productivity, with companies using structured knowledge management for onboarding seeing 62% higher productivity in new hires
- Reduced training costs as employees can learn at their own pace with less direct supervision
- Consistent training experiences across all locations and departments
- Preservation of institutional knowledge from experienced employees
- Enhanced employee satisfaction and retention, addressing the challenge that 50% of manufacturers cite "attracting and retaining a qualified workforce" as a major growth obstacle
Onboarding is more than just a smile and a swag bag
Onboarding isn’t always smooth sailing. So, what are the roadblocks you might hit, and more importantly, how can you bulldoze right through them? Information overload: How much is too much? Ever seen a new hire’s eyes glaze over on day one? It’s probably information overload. You’re trying to equip them with everything they need, but it can be overwhelming. The fix: Break it down. Spread out information over days or weeks. Use tools like Seraf for easy access to information when they need it, not just when you think they need it.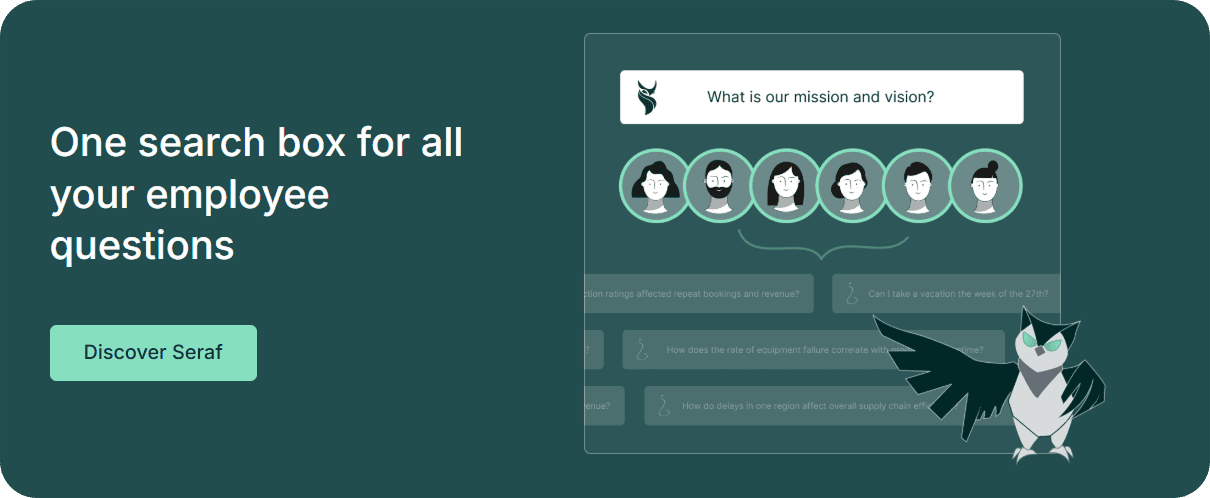